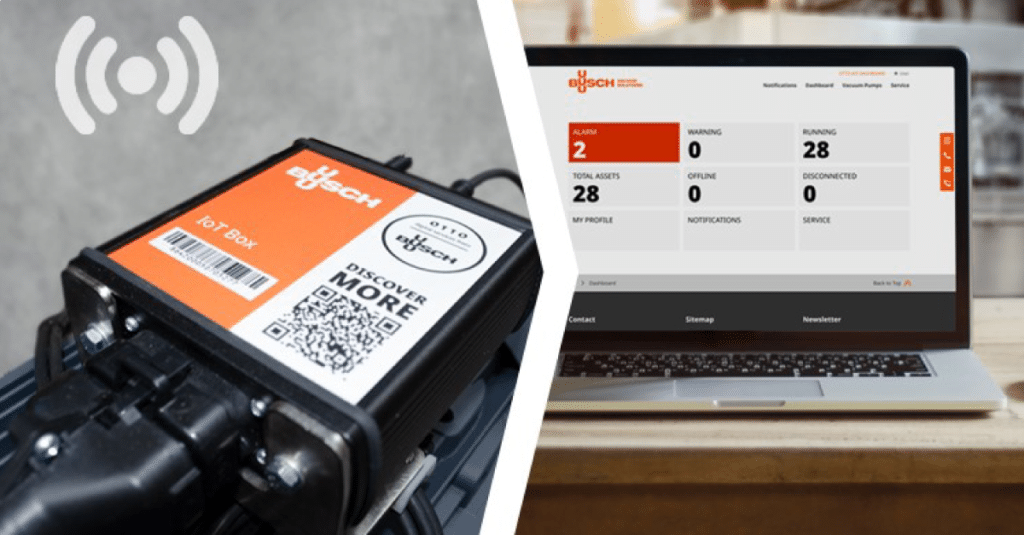
Przestój podczas produkcji w fabryce to znaczący i kosztowny problem i należy zapobiegać jego wystąpieniu. Inteligentne rozwiązania IoT mogą pomóc w redukcji czasu przestoju i wpłynąć na znaczące oszczędności. OTTO to innowacyjna usługa cyfrowa firmy Busch Vacuum Solutions. Łączy monitorowanie stanu pomp próżniowych z atrakcyjnymi pakietami usług. Zapewnia to większą niezawodność procesu i obniża koszty w zakładach produkcyjnych.
Pulpit nawigacyjny IoT firmy Busch i aplikacja Busch Vacuum App stale śledzą dane dotyczące pomp. Dzięki zebranym informacjom można analizować parametry i optymalizować proces. Dane są przechowywane w chmurze Busch za pośrednictwem połączenia mobilnego. Urządzenie IoT box stale monitoruje stan procesu i warunki pracy pomp próżniowych. Są to na przykład temperatura otoczenia, temperatura oleju i czas pozostały do kolejnej konserwacji pompy próżniowej.
OTTO wykrywa potencjalne problemy, zanim staną się one rzeczywistością. Pozwala to na uniknięcie ryzyka i kosztów związanych z nieplanowanymi przestojami. Czas przestoju w produkcji to jedno z największych zagrożeń w branży produkcyjnej. Od awarii sprzętu po braki surowców: każdy czas przestoju w produkcji może skutkować znacznymi stratami w przychodach i udziale w rynku.
Dlatego zapobieganie przestojom w produkcji ma kluczowe znaczenie dla zapewnienia produktywności.
Zachęcamy do postępowania zgodnie z naszymi siedmioma wskazówkami, aby skrócić czas przestoju maszyn na linii produkcyjnej.
1. Opracowanie systemu szybkiego identyfikowania i rozwiązywania problemów produkcyjnych
System powinien gromadzić i analizować dane, które zapewniają wgląd w całościowe wymagania konserwacyjne sprzętu. Interpretacja danych może pomóc pracownikom w rozwiązaniu problemów produkcyjnych poprzez przeprowadzenie konserwacji zapobiegawczej. Wdrożenie takiego systemu pozwala zakładom produkcyjnym na skrócenie czasu przestojów spowodowanych problemami produkcyjnymi i zapobieganie kosztownym nieplanowanym przestojom, dzięki ostrzeganiu pracowników o potencjalnych zbliżających się awariach sprzętu.
2. Wykorzystanie analityki predykcyjnej do identyfikacji potencjalnych problemów jeszcze przed ich wystąpieniem
Analityka predykcyjna wykrywa w czasie rzeczywistym wzorce w danych maszynowych, które mogą prowadzić do wystąpienia problemu. Analizując dane można uzyskać informację z kilkutygodniowym wyprzedzeniem, które części maszyny mogą ulec awarii. Pozwala to zaplanować harmonogramy konserwacji i zamówić części zamienne z wyprzedzeniem, skutecznie skracając czas przestoju i zmniejszając prawdopodobieństwo ponownego wystąpienia problemów.
3. Wdrożenie programu konserwacji zapobiegawczej
Programy konserwacji zapobiegawczej są jednym z najskuteczniejszych sposobów na zminimalizowanie nieplanowanych przestojów maszyn. Można rutynowo zbierać cenne informacje na temat swojego sprzętu, aby zapewnić systematyczne podejście do konserwacji. Odpowiednio ukierunkowana konserwacja umożliwia reagowanie na przewidywane awarie sprzętu lub wypadki, zanim do nich dojdzie. Dzięki ograniczeniu ryzyka nieoczekiwanych czasów przestoju pracownik może skupić się na bardziej dochodowych zadaniach.
4. Stworzenie systemu radzenia sobie z usterkami i problemami w miarę ich pojawiania się
Posiadanie systemu, który śledzi i monitoruje usterki w miarę ich pojawiania się, pozwala na zidentyfikowanie pierwotnej przyczyny problemu na linii produkcyjnej. Można dzięki temu zrozumieć, w jaki sposób dochodzi do awarii produkcyjnych i jak zapobiec ich ponownemu wystąpieniu. Ogranicza to nieplanowany czas przestoju maszyny, zwiększając jednocześnie wydajność produkcji.
5. Automatyzacja jak największej liczby procesów w celu zmniejszenia liczby błędów ludzkich
Można skrócić czas przestoju i zwiększyć wydajność procesu produkcyjnego, automatyzując powtarzalne i żmudne zadania, które są podatne na błędy człowieka. Dzięki temu pracownicy będą mieli więcej czasu, aby skupić się na dochodowych zadaniach i rozwijać swoje umiejętności, co przełoży się na większe zyski firmy i pokaże pracownikom, że są najcenniejsi.
6. Szkolenie dla użytkowników w zakresie prawidłowej obsługi sprzętu
Szkolenie dla użytkowników w zakresie prawidłowego użytkowania sprzętu może znacznie skrócić czas przestoju w procesie produkcyjnym. Jeśli operatorzy wiedzą, jak prawidłowo używać sprzętu, rzadziej zatrzymują produkcję i mogą szybciej reagować w sytuacjach awaryjnych. Odpowiednie szkolenie zapobiega również nieplanowanym przestojom spowodowanym błędami ludzkimi i zmniejsza ryzyko wypadków w miejscu pracy.
7. Korzystanie z inteligentnych rozwiązań IoT
Czy sześć wskazówek to za dużo? W takim razie można skorzystać ze wskazówki nr 7, aby uzyskać rozwiązanie typu „wszystko w jednym”!
Inteligentne rozwiązania IoT pomagają skrócić czas przestoju dzięki systemowi, który umożliwia szybką identyfikację i rozwiązywanie problemów produkcyjnych (wskazówka 1). Monitoruje i śledzi sprzęt i proces za pomocą analityki predykcyjnej, pozwalając tworzyć harmonogram konserwacji i zamawiać niezbędne części zamienne z wyprzedzeniem (wskazówka 2). Czujniki i analityka danych umożliwiają IoT ciągłe śledzenie i monitorowanie danych dotyczących wydajności i optymalizacji. Pozwala to wdrażać konserwację zapobiegawczą (wskazówka 3) i przewidywać potencjalne problemy w miarę ich pojawiania się (wskazówka 4), co skutecznie zmniejsza częstotliwość planowanych lub nieplanowanych czasów przestoju. IoT umożliwia również automatyzację zadań, skracając czas ich realizacji, a w rezultacie zwiększając produktywność i zmniejszając liczbę błędów ludzkich (wskazówka 5). Dzięki przyjaznym dla użytkownika narzędziom łatwo nauczyć się obsługi IoT. Pracownicy w krótkim czasie będą w stanie prawidłowo z niego korzystać (wskazówka 6).
Może warto zoptymalizować swój proces, instalując system IoT?
Busch Polska Sp. z o.o.
www.buschvacuum.com