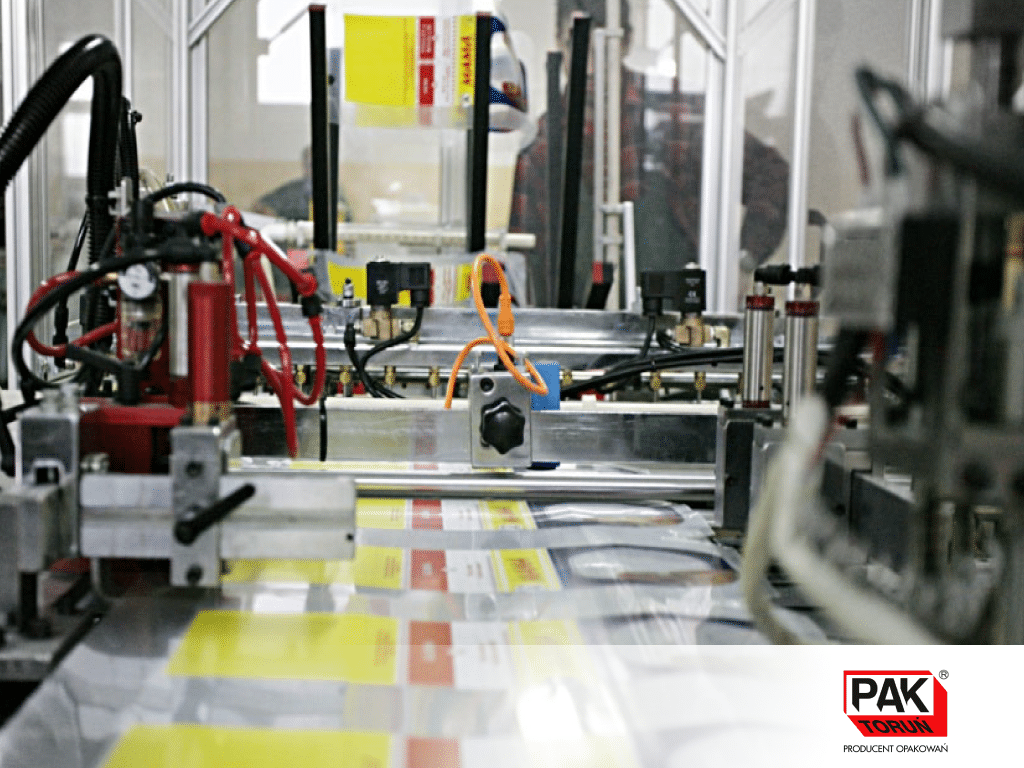
Z Sylwestrem Popławskim, Kierownikiem produkcji Firmy Handlowo-Produkcyjnej PAK Sp. z o.o. rozmawia Marek Bielski
Co należy rozumieć pod hasłem „prawidłowa jednostka paletowa”?
Prawidłową jednostkę paletową charakteryzuje zwarte ułożenie nawojów na palecie. Nawoje nie wystają poza jej obrys, warstwy są równo nawinięte, między warstwami nie ma przesunięć, a wszystkie przełożone są przekładkami. Całość jest ostreczowana i zabezpieczona przed zamoknięciem folią ochronną. Każda paleta powinna również posiadać etykietę identyfikacyjną i dokument WZ.
Jak należy sprawdzać, czy paleta spełnia nasze wymogi?
Podczas przyjęcia na zakład należy sprawdzić zgodność dokumentu WZ z etykietą paletową, stan zabezpieczenia folią ochronną, nawinięcie nawojów – czoło nawojów oraz prawidłowe oznaczenie etykietą na zewnątrz i wewnątrz nawoju.
Dlaczego etykieta powinna znajdować się również wewnątrz nawoju?
Jeśli nawój jest na maszynie, etykieta zewnętrzna znajduje się w dokumentacji. Gdy zdarzy się tak, że nawój przechodzi ze zmiany na zmianę, to w razie wątpliwości, jest możliwość sprawdzenia etykiety znajdującej się w środku. To właśnie ona jest podstawą reklamacji. Etykieta nawojowa pozwala na szybką identyfikację partii produkcyjnej w przypadku potencjalnej reklamacji, analizę potencjalnych przyczyn niezgodności, a często także identyfikację bliźniaczych nawojów mogących mieć podobne cechy.
Jak ocenić folię na wstępnym etapie?
Ocena wyglądu folii na wstępnym etapie obejmuje identyfikację potencjalnych zabrudzeń, uszkodzeń i widocznych zmarszczeń. Należy sprawdzić, czy nawój nie nosi oznak uszkodzenia mechanicznego podczas transportu. Tego typu uszkodzenia mogą wprowadzić zanieczyszczenia do warstw wewnętrznych i przyczynić się do potencjalnych problemów i rwania folii podczas odwijania i procesu pakowania. Zmarszczenia folii – zarówno poprzeczne, jak i wzdłużne również są niepożądane. Oprócz obniżenia walorów estetycznych, mogą być przyczyną nieszczelności. Gilza powinna być równa z nawojem, (dopuszczalna jest tolerancja na poziomie +/- 1 mm), być czysta, sucha, niezdeformowana, bez zapachu pleśni czy jej śladów.
Co należy robić w przypadku, kiedy nawój jest w krytycznej sytuacji?
Zgniecenie gilzy może powstać na skutek upadku nawoju z wysokości. Jego skutki to, oprócz zabrudzenia nawoju również jego odkształcenie, które może utrudnić lub uniemożliwić założenie nawoju na odwijak maszyny. Gilza może także zapaść się pod wpływem wilgoci. Przy przechowywaniu materiałów należy pamiętać, że materiał nie może być kładziony bezpośrednio na posadzkę czy elementy wilgotne. Luźne, teleskopujące nawoje mogą mieć różną genezę – folia może być bardzo śliska, a grafika asymetryczna. Innym niebezpieczeństwem jest także to, że gilza po długim okresie przechowywania może wyschnąć, przez co jej średnica może się nieco zmniejszyć. W tym miejscu może występować luz, który może skutkować teleskopowaniem i problemem przy odwijaniu. Tego typu problemy mogą również wynikać z błędów drukarni. Takie nawoje drukarnia może reanimować z wykorzystaniem dysków stabilizujących. Odbywa się to kosztem wycięcia potencjalnych, trwałych zagnieceń.
W jaki sposób łączy się nawoje w drukarni?
Nawoje łączymy poza znacznikiem fotokomórki, łączymy znacznik-znacznik tak, żeby nie było problemu na maszynie pakującej. Dzięki temu proces pakowania będzie następował płynnie i bez problemów. Łączenia mogą być wykonane różnymi kolorami taśm, w tym również przy użyciu taśmy metalizowanej, pozwalającej na wykrycie łączenia przez detektor metali na maszynie pakującej.
Czy możliwe jest łączenie na kilka torów?
Tak, drukarnie realizują druki na dwa, trzy lub nawet cztery czy więcej torów w zależności od wzoru, nakładu i szerokości maszyny. Ważne jest, żeby łączenia dla klienta realizować tak, by nie zakrywały znaczników fotokomórki.
Jak przeprowadzić pomiar grubości folii?
Na pomiar grubości folii mają wpływ takie czynniki, jak grubość poszczególnych warstw i miejsce pomiaru – czy robimy to w miejscu bezbarwnym, czy na zadruku, dlatego też przy pomiarze dopuszcza się tolerancję 0,005 mm. Dokonujemy go mikromierzami mechanicznym lub elektronicznym. Tolerancja pomiaru wynika również z temperatury, w jakiej się go wykonuje. Mikrometr ręczny ma wahania na poziomie 2 mikronów i taka tolerancja pomiaru folii opakowaniowych jest dopuszczalna.
W jaki sposób prawidłowo wykonać pomiar szerokości?
W tym przypadku wystarczy dobrej klasy linijka, a tolerancja 1-2 mm rzadko jest przedmiotem dyskusji. Folia podczas pomiaru powinna leżeć płasko na stole, być lekko naciągnięta, najlepiej przyklejona dodatkowo taśmą. Nie powinno być pod nią żadnych kartek czy drobinek. Pomiar należy powtórzyć, co daje większą możliwość wychwycenia błędu. Należy również upewnić się, że pomiaru nie dokonujemy po skosie, co dałoby nam zawyżony wynik.
Skok fotokomórki flowpack – dlaczego w tym przypadku możliwa jest duża tolerancja?
Są sytuacje, że z uwagi na koszt polimerów drukarnia uzgadnia z klientem wydłużenie lub skrócenie wzoru nawet o 1-2 cm. Wynika to z indywidualnych uwarunkowań. Takiej możliwości nie mamy w przypadku maszyn rolowych. W przypadku wzorów gniazdowych dokładność pomiarowa na poziomie < 0,5 mm jest kluczowa dla procesu, ponieważ na pozór drobne błędy mogą skutkować niezdatnością wydrukowanego laminatu do procesu pakowania.
Jak zatem można ustrzec się błędów?
Podstawą jest rysunek techniczny – tzw. DSS dla konkretnej formy maszyny i próby produkcyjne. Zaniedbania na etapie wdrażania nowego wzoru, nowej formy czy nowego podziału na maszynie wiążą się z ryzykiem nieprzydatności całej dostarczonej, zadrukowanej partii folii do procesu pakowania. Zarówno za długa odległość między znacznikami, jak i za krótka może wprowadzić chaos na maszynie, a możliwości korekty są w tym przypadku zazwyczaj bardzo ograniczone.
Czy możemy rozróżnić folie ze względu na ich rozciągliwość?
Tak. Producenci maszyn rozróżniają folie rozciągliwe, średniorozciągliwe i nierozciągliwe oraz podają dla nich tolerancję powtarzalności na odcinku 1 metra. Do folii najmniej rozciągliwych należą folie oparte na konstrukcji PET/ PE, nieco bardziej rozciągliwe są folie z BOPA/PE, a najbardziej elastyczne będą konstrukcje z wykorzystaniem polipropylenu z polietylenem albo samego polietylenu.
Jak sprawdzić czytelność kodu kreskowego?
Jakość i dekodowalność kodu kreskowego drukarnia sprawdza weryfikatorem kodów kreskowych. Używanie do tego celu skanerów czy aplikacji w telefonie to półśrodek nie polecam takiej weryfikacji, ponieważ nie gwarantuje nam odczytania kodu przez inne skanery. Ważna uwaga – kreski powinny być drukowane wzdłuż druku lub wzdłuż rozwijanej wstęgi na maszynie, nigdy w poprzek. Istnieje bowiem ryzyko nieczytelności kodu. Najlepiej jest też, aby kod był drukowany kolorem czarnym, na białym podkładzie. Niedopuszczalne jest drukowanie kresek ze złożenia kolorów. Zbyt małe kody, za wąskie marginesy lub ich brak, wszystko to powoduje, że kod może być nieczytelny.
Na co należy zwrócić szczególną uwagę podczas oceny zadruku?
Absolutne priorytety dla wzoru oraz jego oceny i odbioru to jego czytelność, zgodność tekstu oraz kodu kreskowego ze wzorem. Jeśli zdarzy się, że grafika będzie odrobinę rozjechana, nic się nie stanie, jeśli natomiast pojawi się błąd w tabeli lub w kodzie kreskowym, wtedy cała partia towaru może iść na śmietnisko. Spasowanie grafiki stawiam więc na drugim miejscu.
Z jakimi najczęstszymi wadami druku mamy do czynienia?
Najczęściej mamy do czynienia z plamami, przebarwieniami i kreskami. To są rzeczy, na które należy zwrócić uwagę oraz ocenić czy, i w jakim stopniu, nam przeszkadzają. Należy przy tym pamiętać o tym, że w przypadku druku fleksograficznego wstęga na maszynie drukarskiej drukowana jest z prędkością 200 – 400 metrów/minutę. Drukarz, gdy pojawi się problem, musi zadecydować, kiedy zatrzymać maszynę, bo skutkuje to łączeniami w nawoju, tak nielubianymi przez operatorów maszyn pakujących.
Czytelny tekst to również ważny element…
Zgadza się. Czarny mikrodruk na białym tle będzie zniechęcać do czytania, ale przy pomocy lupki sobie poradzimy. Natomiast drobny, biały tekst na ciemnym tle złożonym z kilku kolorów może okazać się zupełnie nieczytelny. Tu musimy słuchać sugestii drukarzy. Ich uwagi są cenne i pozwolą na osiągnięcie lepszych rezultatów.
W jaki sposób można dokonać oceny wizualnej zadruku?
Ocena wizualna jest niezbędna, ale pozostaje subiektywna. Ludzkie oko jest w stanie rozróżnić ponad 10 mln kolorów, przy czym postrzeganie kolorów zmienia się wraz z wiekiem. Są też badania, które wykazują wyższość płci żeńskiej w widzeniu kolorów. Pamiętajmy też, że kolorystyka może zmieniać się w zależności od oświetlenia. Najlepiej jest oceniać zadruk w świetle znormalizowanym D50, zbliżonym do światła dziennego. Nie oceniamy w pełnym słońcu. Kąt obserwacji jest mniej istotny. Przy ocenie wzoru graficznego na monitorze należy mieć na względzie fakt, że wydruk na folii może wyjść gorzej, przykładowo może być zmatowiały, mało wysycony czy nieostry. Musimy zdawać sobie sprawę z różnic – RGB to kolory na monitorze, a CMYK to wydruk farbami na folii. Do oceny kolorów specjalnych – pantonów – stosujemy standard w postaci palety barw pantone. Wzorniki pantonowskie służą nam jako referencja, żeby widzieć, jak dany kolor wygląda. Choć wykorzystujemy wydrukowane wzorniki kolorystyczne to dla bezpieczeństwa i obiektywnej oceny kierujemy się wskazaniami spektrofotometru jako wzornikiem cyfrowym z wbudowaną biblioteką barw. Najpewniejszym wyznacznikiem jest kolor zmierzony cyfrowo. Spektofotometr, będący zaawansowanym narzędziem kolorymetrycznym daje między innymi możliwość liczbowego określenia różnicy między dwoma porównywanymi kolorami, czy też wzorcem i próbką albo proofem i wydrukiem.
Poza walorami estetycznymi wzoru kluczowe pozostają aspekty techniczne jak znacznik fotokomórki. Powinien on być jednolicie wydrukowany, a odległości między kolejnymi znacznikami idealnie zachowane. Należy pamiętać, że szerszy znacznik, jest bezpieczniejszy dla maszyny pakującej. Jego wysokość nie jest aż taka istotna. Gorzej jest, jeśli będzie niedodrukowany i zginie nam kontrast.
Czym są problemy z delaminacją?
Delaminacja to prawdziwy koszmar dla operatorów laminacji. Problem z laminatami jest taki, że podczas procesu produkcji operator ma niewielką szansę na stwierdzenie czy laminat będzie z pewnością wolny od wad. Wstępny efekt widać najszybciej po godzinie pracy. Delaminacja oznacza automatycznie reklamację. W takiej sytuacji, trzeba zabezpieczyć fizyczną próbkę i zadbać o dobre zdjęcie wady i etykiety. Na podstawie zdjęć i próbki przesłanej kurierem drukarnia będzie w stanie podjąć błyskawiczne działania oraz wyznaczyć nawoje, które mogą mieć tę samą cechę. Delaminacja może mieć różną naturę. Może wystąpić w całej partii, w 2-3 nawojach, na kilku – kilkunastu metrach, po sklejce albo przed sklejką. Jej przyczyny mogą być różne. Jeśli mamy do czynienia z brakiem aktywacji, wtedy delaminacja następuje na całej szerokości folii. Warto wiedzieć, że problem, jakim jest brak aktywacji może zacząć się nieoczekiwanie i tak samo nieoczekiwanie skończyć, a jego przyczyną może być chociażby chwilowy zanik prądu, którego nawet nie dostrzeżemy. Jeśli natomiast chodzi o odbiór wizualny, tzw. problemy z optyką: bąble, pęcherze, skórka pomarańczy, ich przyczyny mogą być różne. Mogą wynikać ze zbyt małej lub zbyt dużej ilości kleju, niekorzystnymi warunkami jego sieciowania; mogą być związane z cechami fizycznymi folii, z warstwami funkcyjnymi znajdującymi się w środku, z oddziaływaniem kleju na farbę i farby na klej. Dodatkowo, warstwa funkcyjna EVOH może ulegać degradacji i będzie to widoczne najczęściej pod działaniem wysokiej temperatury, przy pełnych płytach grzewczych na maszynach rolowych czy zgrzewarkach cateringowych. Przykłady, co do których mamy wątpliwości, warto wysłać do drukarni, która je oceni.
Jakie są własności użytkowe folii?
Jest ich wiele. Do kluczowych należy barierowość na tlen, i parę wodną, czy powłoki funkcjonalne jak warstwa antyfog, zapobiegająca zamgleniu powierzchni od strony produktu. Warstwa zgrzewalna easy peel czy easy open, to nie klej, lecz cechy zgrzewalne folii. Folia czy laminat może mieć obie lub jedną stronę zgrzewalną, przykładowo konstrukcja typu PET/ PE czy BOPA/PE będzie miała jedną stronę zgrzewalną – polietylen. Standardowo, powierzchnia zgrzewalna folii czy laminatu nawinięta jest do wewnątrz nawoju. Tak postępuje większość dostawców drukowanych opakowań. Jeżeli mamy do czynienia z folią drukowaną, to bardzo łatwo jest rozpoznać, która strona jest zgrzewalna i czy drukarnia nawinęła właściwie materiał. Problem będzie trudniejszy do zdiagnozowania w materiałach bezbarwnych. Klient ma wtedy mniejsze możliwości sprawdzenia, która strona folii jest warstwą zgrzewalną.
Jak w takim razie rozwiązać ten problem?
Pomocne będą proste zgrzewarki z drutem kantalowym. Są ogólnie dostępne i bardzo szybko pomagają oznaczyć stronę zgrzewalną. Operatorzy z doświadczeniem wiedzą, że za niska temperatura pakowania skutkuje nietrwałym lub nieszczelnym zgrzewem lub brakiem zgrzewu w ogóle, za wysoka natomiast może skutkować przepaleniem folii. Nowe konstrukcje, formy czy maszyny musimy testować do wyznaczenia optymalnych parametrów. Pamiętajmy przy tym, że aktywacja folii nie równa się stronie zgrzewalnej. Aktywacja służy do druku i laminacji, a strona zgrzewalna powinna być jej pozbawiona.
Jak należy przechowywać folie?
Folie powinny być przechowywane w suchym, zacienionym magazynie, przy wilgotności 30-65%. Przy wyższej wilgotności przykładowo konstrukcja BOPA/PE staje się tępa, inaczej pracuje na maszynie, zaczyna trzeszczeć i uciekać z prowadzenia. Ponadto, przy zamoknięciu mogą puchnąć gilzy nawojowe, czego konsekwencją będą trudności z nałożeniem nawoju na odwijak maszyny, gilzy odkształcą się i mogą się zapaść. Oczywiście, drukarnie są w stanie taki materiał przewinąć i nawój można uratować. Jeśli natomiast chodzi o temperaturę, optymalne jest przechowywanie folii w temperaturze 5 – 25oC. Poniżej tej temperatury elastyczność folii spada, folia staje się krucha, podatna na przebicie i przerwanie. W temperaturach wyższych niż zalecane z politylenu wychodzą środki poślizgowe na zewnątrz, nawój może stać się śliski i teleskopować. Należy też pamiętać, że folii nie przechowujemy również w pełnym słońcu. Nadruk na folii wystawionej na działanie promieni słonecznych ulegnie odbarwieniu a sama folia, po wymigrowaniu z niej plastyfikatorów może stać się krucha.
Jaki jest czas przechowywania folii?
Większość folii może bezpiecznie stać na regałach 1- 3 lata bez utraty jakości. Folie z antyfogiem, poza wyjątkami, mają natomiast 3 miesiące gwarancji.
Jaki mikrometr najlepiej sprawdzi się do pomiarów grubości folii?
Do pomiarów nadają się zarówno mikrometry mechaniczne, jak i cyfrowe, przy czym oba wymagają prostej, ale częstej kalibracji na zero. Aby pomiar był wiarygodny, należy go wykonać kilka razy i w wielu miejscach. Trzeba też zadbać o to, żeby folia w miejscu pomiarów nie była pognieciona, a mikrometr osiągnął temperaturę panującą w miejscu pomiaru. Pamiętajmy, że pomiar ma pewną tolerancję.
Czy istnieje sposób by sprawdzić delaminację warstwy EVOH bez specjalistycznych narzędzi?
Jeżeli następuje delaminacja warstwy EVOH wystarczy zmierzyć mikromierzem dwie zdelaminowane warstwy. Znając deklarowaną grubość jednej i drugiej, będziemy w stanie stwierdzić, czy delaminacja nastąpiła na którejś warstwie folii polietylenowej. Warstwa EVOH w polietylenie będzie wkomponowana w ten sposób, że będzie z jednej i drugiej strony okryta klejem, ponieważ polietylen z EVOH nie wiąże się w sposób ścisły bez kleju. W takich warstwach wielu producentów stosuje warstwy poliamid – EVOH – klej – polietylen. Możliwych rozwiązań jest jednak znacznie więcej.
Jak ma się temperatura przechowywania folii do przechowywania mięsa w warunkach chłodniczych?
Jak powiedziałem wcześniej, folię w magazynie przed pakowaniem powinno się przechowywać w temp 5-25OC. Jest to dla niej optymalna temperatura. Po pakowaniu można przechowywać ją w temperaturze przez nas pożądanej. Warto jednak pamiętać, że jeżeli temperatury będą oscylować w granicach -30oC do – 80oC produkty należy przechowywać bez wstrząsów, inaczej na folii mogą nastąpić mikropęknięcia czy rozerwania.
Jaka grubość folii jest dedykowana do mrożenia produktów?
Przede wszystkim najlepiej w takich warunkach sprawdzi się folia czy laminat polietylenowy, który daje najlepsze właściwości mechaniczne i zgrzewalne. Grubość folii jest sprawą drugorzędną i będzie zależna od masy zapakowanego produktu, a także jego kształtu i sposobu pakowania. Ostre zmrożone elementy spadające z wysokości w formowane opakowanie będą wymagały, prócz grubości również folii specjalnie modyfikowanej. Z reguły grubości oscylują w okolicach 60-90 mikronów.
Czy folie mają termin ważności?
Naszym klientom dajemy roczną gwarancję od daty dostawy materiału. Wszystko zależy jednak od doboru surowca, z którego laminat został wyprodukowany. Folie z powłoką antyfog mają krótszy termin ważności wynikający z nietrwałości działania tego dodatku w czasie. Folie bez antyfogu – PET/ PE, PA/PE wytrzymują bardzo długo, w dobrych warunkach magazynowania i 20 lat może nie być zaskoczeniem. Oczywiście, przy dłuższym czasie przechowywania folie żółkną, tracą swoje środki poślizgowe, elastyczność i stają się coraz bardziej kruche. Niektóre polipropyleny po kilku latach przechowywania mogą się rozpaść w rękach i nie ma to nic wspólnego z biodegradowalnością.
W jaki sposób można sprawdzić delaminację laminatów OPP/OPP?
Laminaty te są najprostsze w produkcji. Można je skleić niemal każdym typem kleju. Jeżeli warstwy możemy swobodnie rozłożyć, to sprawa jest prosta, albo zabrakło tam kleju, albo któraś z warstw nie ma minimalnego poziomu aktywacji niezbędnego do procesu laminacji. Rozstrzygnięcie w tym przypadku przyniesie weryfikacja specjalnym testerem aktywacji.
W przypadku wątpliwości możemy zgrzać opakowanie na zgrzewarce kantalowej i spróbować wówczas ten zgrzew rozerwać. Jeżeli laminat rozchodzi się poprzez rozrywanie, dopiero po przyłożeniu pewnej siły to może okazać się że delaminuje się któraś z warstw folii polipropylenowych. Pamiętajmy, że folia polipropylenowa może mieć 3 lub 5 warstw składowych plus uszlachetniające powłoki. W takim przypadku znów można posiłkować się pomiarem grubości zdelaminowanych, czy rozerwanych warstw.
Z czym może być związany problem delaminacji w przypadku, kiedy laminat nie wykazuje problemów i jest w terminie przydatności, a opakowanie z tego laminatu wykazuje delaminację podczas procesu otwierania?
Tu może być kilka wersji odpowiedzi. Poliester jest folią sztywną, a polietylen – miękką i elastyczną, folie te mają skrajnie różne własności rozciągania. Delaminacja może również nastąpić między pewnymi funkcyjnymi warstwami polietylenu, np. na warstwie EVOH, czy easy peel. Może więc okazać się, że rozerwiemy folię samą w sobie.
Jak często powinniśmy żądać od producenta folii deklaracji zgodności?
Przy każdej dostawie. Do każdego dokumentu WZ wystawiamy ogólną deklarację zgodności / świadectwo jakości, na którym widnieją numery partii towaru niezbędne do potrzeb identyfikowalności. Pełna deklaracja zgodności wystawiana jest okresowo, na prośbę klienta i ważna jest do momentu zmiany przepisów prawnych lub zmian w procesie technologicznym. Wystawiony dokument poświadcza przeprowadzoną kontrolę towaru min. pod kątem jakości zadruku, szerokości, grubości i potencjalnej delaminacji.
Jaka grubość folii dedykowana jest do produktów z kością?
Do pakowania na maszynach rolowych bezpiecznie będzie użyć PAPE o grubości 100 mikronów jako folii górnej, PAPE 200-250 jako folii dolnej, schodzenie z grubością każdej folii wymaga testów i a wyniki będą uzależnione od maszyny, podziału, i rodzaju pakowanego produktu. Warto porozmawiać z handlowcami, przeprowadzić próby by dobrać optymalne grubości.
Czy na rynku dostępne są folie z filtrem UV?
Tak. Na rynku dostępne są lakiery z filtrem UV, którymi można zadrukować folie i uzyskać zadowalający efekt. Minusem tego rozwiązania są nakłady. Dostawcy lakierów z filtrem UV sprzedają ten produkt w 200 litrowych beczkach, co przekłada się na sens ekonomiczny w przypadku naprawdę sporych i regularnych zamówień. Najlepszym i najtańszym filtrem jest więc zadrukowanie folii.
Czy kolor zadruku wpływa na barierowość i przechowywanie produktu finalnego?
Nie sądzę, żeby dla barierowości opakowania, poza metalizowaną powłoką, kolor miał jakiekolwiek znaczenie. Jeżeli natomiast weźmiemy pod uwagę samą folię opakowaniową, czy laminat, z nadrukiem to należy pamiętać, kolory typu czerwienie, żółcie i granaty z czasem bledną. Sugerujemy więc przechowywanie ich w zacienionych miejscach.
Jaka folia dla produktów mięsnych przeznaczona jest do recyklingu?
Do recyklingu najlepiej nadają się monomateriały, czyli konstrukcje oparte tylko na PET albo wyłącznie na polietylenach czy polipropylenach. Dopuszcza się też mieszanki polietylenu z polipropylenem, tzw. poliolefiny.
Dziękuję za rozmowę.
Oprac. Katarzyna Salomon
Zapis webinaru „Folie opakowaniowe – zagadnienia jakościowe” , który odbył się w dniu 5 maja na platformie MEATplace.pl