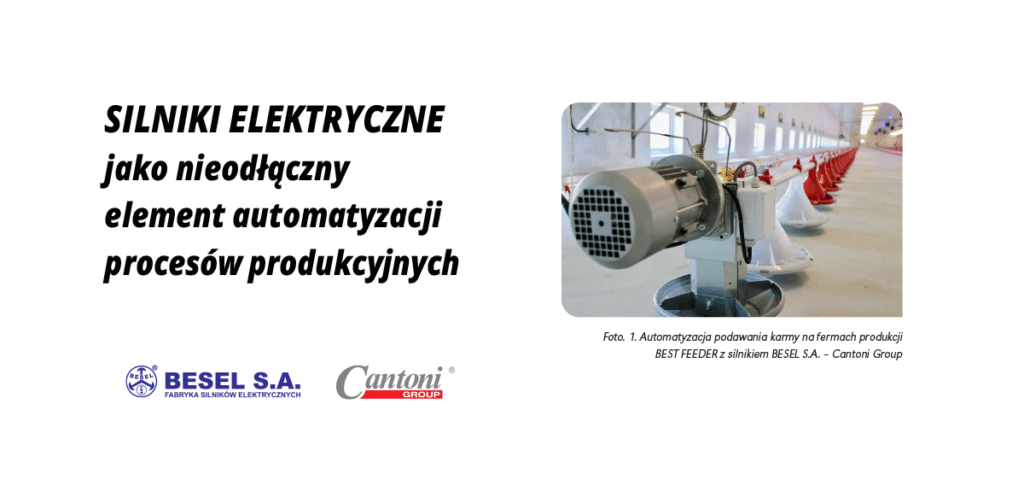
Szeroko pojęta branża spożywcza to wciąż bardzo szybko rozwijająca się gałąź przemysłu. W czasach gdy koszty wytworzenia stanowią często „być albo nie być” dla producentów, coraz bardziej znaczącą rolę odgrywa automatyzacja procesów wytwórczych. Nieodłącznym elementem automatyzacji jest element wprawiający w ruch, którego podstawą jest silnik elektryczny.
Ostatnie lata w tym obszarze można uznać za przełomowe. Popularyzacja układów sterowania, szczególnie tych uwzględniających regulację prędkości obrotowej sprawiła, że możliwości zastosowania silników elektrycznych zwiększają się bardzo szybko. Wzrastają możliwości, ale i wymagania stawiane całym napędom i ich poszczególnym elementom.
Dominują przede wszystkim napędy wykorzystywane w transporcie. Napędy stosowane w transporcie wewnątrzzakładowym, pomiędzy procesami, nie różnią się zbytnio od napędów stosowanych w innych branżach. Jest jednak jedna cecha, która jest dla branży spożywczej bardzo specyficzna. Chodzi o kwestie higieny i ogólnego utrzymania czystości w procesie. W takich przypadkach napędy stosowane w transporcie żywności muszą charakteryzować się możliwością łatwego czyszczenia, a wręcz bezpośrednio mycia. Stąd wykorzystywanie stali nierdzewnej jako elementów obudowy silników, a także unikanie skomplikowanych, wielopłaszczyznowych konstrukcji. Upraszczając: silnik powinien być gładki, odporny na korozję, szczelny, a jego parametry dostosowane do ograniczonych warunków chłodzenia (brak żeber radiacyjnych).
Środowisko w zakładach produkcji żywności często nie jest najkorzystniejsze dla elementów standardowo stosowanych jako obudowy silników elektrycznych. Szczególnie w przypadkach hodowli zwierząt, gdzie instalacje mogą mieć styczność choćby z agresywnymi chemicznie czynnikami (np. odchody zwierząt). W takich przypadkach zabezpieczenia antykorozyjne i elementy uszczelniające wnętrze silnika odgrywają kluczową rolę. Możliwe jest także w razie konieczności zastosowanie specjalnego malowania (epoksydowe) czy galwanizowania (np. cynkowanie) (Foto. 1.).
Innym sposobem na zabezpieczenie napędu przed szkodliwym działaniem otoczenia może być zamknięcie silnika w obudowie urządzenia. Temat wymaga najczęściej ścisłej współpracy producenta napędu z producentem aplikacji, ponieważ silnik musi „wpasować się” w urządzenie bądź dział rozwoju produktu już na etapie projektowania musi przewidzieć ile miejsca zajmie napęd.
W tym przypadku, nawet bardziej niż przy silnikach bez radiatora, istotne jest zapewnienie odpowiedniej rezerwy cieplnej obwodu elektromagnetycznego lub też dodatkowego chłodzenia. Silnik zamknięty w szczelnej obudowie nie ma bezpośredniego chłodzenia powietrzem. Nawet zastosowanie przewietrznika pozwala jedynie na mieszanie nagrzanego powietrza wewnątrz obudowy.
Przykład takiej aplikacji stanowić może krajalnica firmy „MaGa” z Bydgoszczy, z silnikiem BESEL S.A. zabudowanym wewnątrz obudowy. Pewną zaletą może być brak konieczności wyposażenia silnika w obudowę własną (korpus) czy stosowanie własnego wentylatora co czasem może wpłynąć na optymalizację kosztów produkcji.
Na wstępie wspomniana została coraz większa popularność napędów z użyciem przemiennika częstotliwości. Takie rozwiązanie pozwala na dostosowanie prędkości obrotowej silnika do rzeczywistych potrzeb aplikacji w danym momencie. Może też redukować negatywny wpływ bezpośredniego rozruchu (soft-start) oraz daje możliwość wykorzystania wielu opcji dodatkowych, w które są wyposażone komercyjne przemienniki (zabezpieczenia, sygnalizacje, zdalne sterowanie). Nie wszystkie przemienniki spełniają wysokie wymagania panujące w obszarach związanych z przetwarzaniem żywności (odporność na czynniki chemiczne, stopień ochrony IPxx itp.) stąd czasem konieczność zintegrowania ich z obudową silnika, czyli upraszczając zamknięcie przemiennika w obudowie silnika spełniającej wcześniej wspomniane wymagania.
Przemienniki częstotliwości niosą jednak ze sobą szereg nie dających się pominąć zagrożeń dla samych silników. Regulacja napięcia wpływa na skuteczność chłodzenia własnego silnika. Jakość napięcia zasilającego, o ile nie stosuje się specjalnych, a co za tym idzie kosztownych filtrów, jest znacząco niższa niż napięcia w sieci wpływając tym samym na parametry silnika. Największym z zagrożeń jest jednak zjawisko powstawania pików przepięciowych, a w konsekwencji wyładowań niezupełnych w uzwojeniach silników zasilanych z falowników. Wyładowania te degradują stopniowo izolację elektryczną uzwojeń finalnie powodując awarie. Niestety falownik nie jest tanim elementem a co za tym idzie, w niektórych przypadkach poszukuje się rozwiązań „budżetowych”. Z naszego (BESEL S.A.) doświadczenia wynika, że im prostszy, a co za tym idzie tańszy przemiennik tym gorsza jakość napięcia zasilającego podawanego na silnik oraz większa podatność napędu na występowanie wspomnianych wyładowań niezupełnych. Zjawisko multiplikuje stosowanie długich przewodów zasilających pomiędzy przemiennikiem a silnikiem akumulujących energię rozładowywaną w postaci pików przepięciowych. Rozwiązań wspomnianych problemów jest wiele: od skracania odległości pomiędzy przemiennikiem a silnikiem, stosowanie filtrów du/dt (kosztowne) po wzmacnianie układów izolacyjnych silników oraz wszelkie kombinacje powyższych. Odporność układu izolacyjnego na piki przepięciowe i powstające w związku z nimi wyładowania niezupełne określa się poprzez klasy IVIC wg normy IEC 60034-18-41. Im dalsza literka w alfabecie, tym wyższa klasa odporności.
W ostatnich latach niezwykle istotnym parametrem stała się efektywność energetyczna (sprawność). Z jednej strony na producentach silników podnoszenie energooszczędności ich wyrobów wymusza Unia Europejska poprzez odpowiednie regulacje definiujące minimalne klasy sprawności jakie muszą spełniać silniki. Z drugiej strony końcowi użytkownicy większy nacisk kładą na zużycie jakże kosztownej energii elektrycznej w swoich przedsiębiorstwach. Nie do pominięcia jest także coraz większa dbałość o środowisko naturalne. Oczywiście tu też otwiera się pole do tzw. indywidualizacji napędu, bo przecież zużycie energii najbardziej istotne jest w napędach pracujących ciągle lub co najmniej długotrwale, a także tam, gdzie napędów jest wiele stanowiąc znaczący udział w zużyciu energii. Co do napędów wykorzystywanych krótkotrwale, sporadycznie, ważne są inne parametry (moment obrotowy, rozruchowy, maksymalny, temperatura na obudowie i wiele innych), a nie zużycie energii podczas tej krótkiej chwili pracy.
Wszystkie wyżej opisane cechy silników elektrycznych stosowanych w szeroko pojętej branży spożywczej wskazują na jeden element, który może okazać się bardzo istotny przy projektowaniu urządzeń i doborze odpowiedniego napędu. Jest to współpraca pomiędzy końcowym użytkownikiem, producentem aplikacji oraz producentem napędu (w tym silnika). Tylko właściwy przepływ informacji o faktycznych wymaganiach w miejscu zainstalowania pomiędzy wspomnianymi stronami pozwala na optymalny dobór napędu. I tu pojawia się przewaga rodzimych producentów tego typu urządzeń. Będąc polskim producentem i posiadając odpowiednie zasoby (dział rozwoju i serwisu na miejscu) BESEL S.A. wielokrotnie uczestniczył w fazie projektowania, wdrażania urządzeń z produkowanymi w swojej fabryce silnikami, a także zawsze oferuje wsparcie techniczne na różnych etapach użytkowania swoich napędów. Korzystając z wielu dekad doświadczeń BESEL S.A. (powst. 1950 r.) oraz indywidualizowanych rozwiązań, nie tylko wspieramy rodzimy przemysł, ale mamy szansę otrzymać produkt doskonale dopasowany do wymagań danej aplikacji, co finalnie zaowocuje satysfakcją końcowego użytkownika, a przecież na tym opiera się każdy biznes.